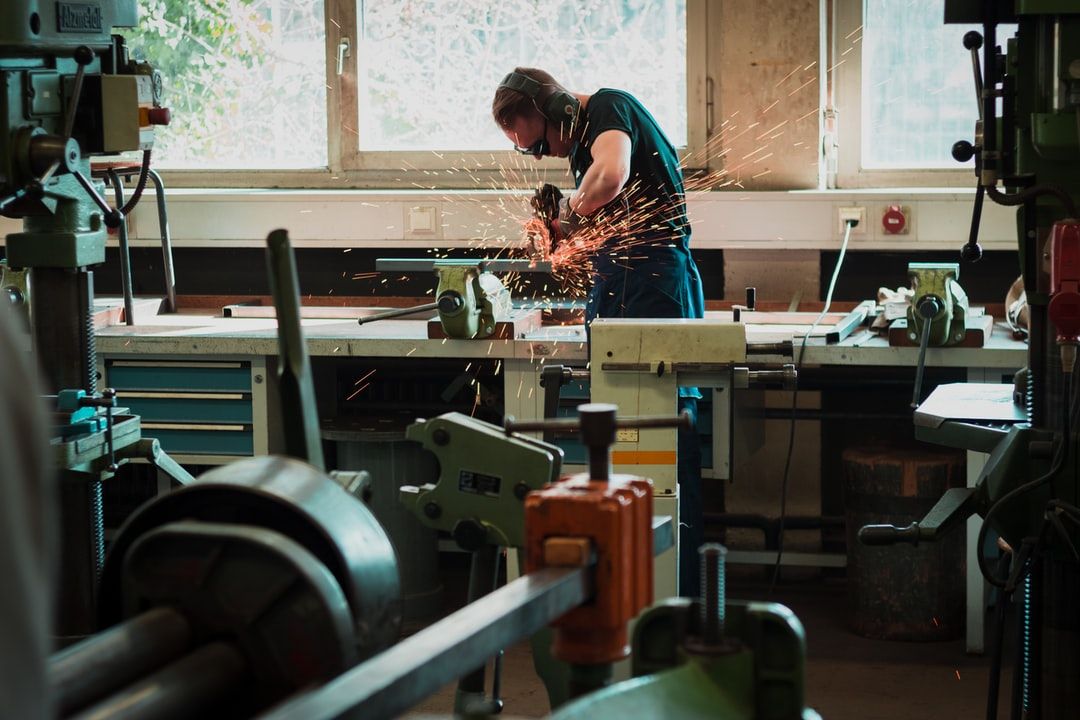
*Real Time Location System
The management of industrial flows consists in organizing the movement of material, or work in progress, during the manufacturing process in order to obtain the best possible performance (productivity, TRS, cycle time, stock, etc.).The degree of complexity varies from one plant to another depending on the number of operations to be carried out, the product mix, the organization of the production space and the logistical constraints imposed by the products; indeed the production constraints for a watch, a car or a one-ton gear are different.
This complexity generates unforeseen situations in the initial planning of operations which materialize in the search for work in progress on site and a lack of overall visibility on the progress of production.
What is the solution today to finish production orders on time?
The responses put in place so far to manage the complexity of the production organization have been of two types:
• Software: The ERP and MES type systems since the 1980s have made it possible to take into account a greater number of criteria in the production organization. It has become possible to manage increasingly complex situations and flows and to be as close as possible to reality.
• Organizational: the gradual development of the Lean approach since the 1950s and more particularly since the late 1990s has made it possible to take into account the reality on the ground in order to adapt to it. This has given rise to the implementation of solutions such as adapting the workstation, U-shaped production lines, reducing unnecessary movements, kanban, taking into account hidden times …
One of the main challenges in deploying ERP / MES solutions is to ensure the perfect match between “physical” and “IT”.
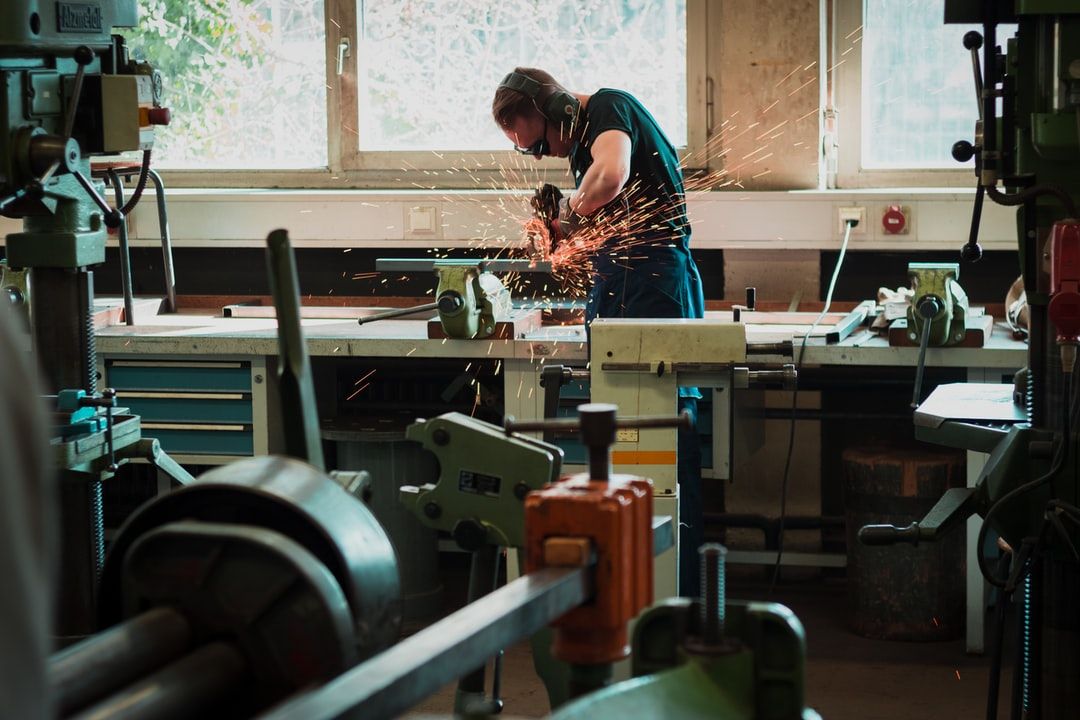
Today there is a mode of organization which allows to gain in efficiency based on the automatic retrieval of the geolocation information of the objects which are important for the production..
Manufacturing can then be organized from real and verified data, making decision-making more efficient: the notion of “management” takes on its full meaning.The timing of tasks and the response to hazards are carried out with up-to-date information and by anticipating the course of the next actions. For example, a workstation starts its operations knowing that in 10 minutes the next batch of parts will be delivered. Or, an operator of a machine tool goes to the next production order because he is informed that the part that was planned at time T is still on the other side of the factory. The conveying of parts can be anticipated as well as the provision of specific tools.
We must add to this location information the possibility of digitally exchanging information with users. Information is made accessible directly where it is used, in the field, without going through a printed document or a workstation.
This organization of production “in real time”, this control, are based on RTLS (Real Time Location System) technologies which are based on the implementation of active or passive identifier (IIoT – industrial IoT) and an infrastructure radio.
The active identifier, equipped with a battery, communicates autonomously with the radio system. It is distinguished from the passive identifier such as the RFID tag which needs to receive an external signal to send back information. There are several radio technologies, those for locating objects (UWB, BLE) and those for communicating over robust industrial radio networks or over very long range / very low power consumption networks like LORA.
Each object to be tracked has an identifier. The object (work in progress / tooling) is taken into account in real time in the organization of production. In order to enhance the data from the sensors, the radio infrastructure is connected to the various business software to exchange the necessary information. The main indoor geolocation technologies have been around for several years which has allowed them to reach a level of maturity and reliability for use in industry.
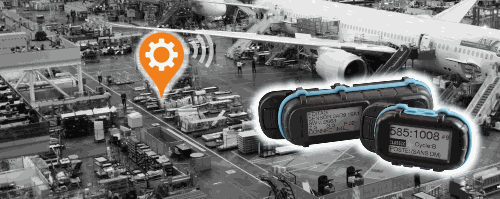
There are currently 3 ways to follow flows:
Triangulation : The object is equipped with an active sensor – the system determines the position of the object in real time (RTLS) relative to antennas whose position is known, such as in UWB technology for example. Very precise, this solution requires however the installation of several antennas to mesh the area of movement of the objects. The implementation costs are the highest compared to other solutions.
Zoning : the object is equipped with an active sensor – a radio beacon, similar to the BLE beacon or a WIFI terminal, emits a periodic signal with an adjustable range. The sensor that receives this signal knows that it has entered the beacon area (a storage location, a production island, a transit point typically); the lack of signal reception lets him know it has gone out. The sensor communicates this information in real time. This solution is the easiest to configure / reconfigure because all you have to do is turn on the beacon in the desired location for the system to be operational. In addition, this system does not require network cabling to operate, which represents a significant saving during the implementation of the solution.
Passage detection : the object is equipped with a passive identifier – the system is made up of RFID gates or passage points which read the identifier at each passage. This solution offers the advantage of being able to operate in environments where active sensors cannot yet go and allow mass identification when there are a large number of objects to be detected simultaneously. There is a very wide choice of inexpensive RFID identifiers capable of functioning in virtually any environment, but the solution requires the installation of gantry cranes in specific locations which can be expensive to implement.
The table below summarizes the different possible approaches:
Portique RFID |
Zoning |
Triangulation | |
Location accuracy | NA | 1m-30m | <1m |
Location type | Waypoints |
Waypoints
Pre-determined points
|
All |
Mass passage detection | + | = | = |
Implementation | = | + | – |
User interaction | NO | YES | YES |
Other sensors (temperature, shock, etc.) | NO | YES | YES |
Each application has its advantages and disadvantages and it is the way of implementing them that gives the final level of performance and value creation of the solution.
Recently, hybrid sensors have appeared which implement several technologies at the same time in order to cover the most widely use cases in the field, and add new functions such as displays, it is a hybrid RTLS solution.
The configuration and needs of each manufacturer are different and even at the heart of the same installation, the needs may vary from one workstation to another. The technological solution must adapt by implementing the right technology at the right time and comply with the needs of the processes and not force the processes to make concessions due to the limits of the technology; as the automatic air conditioning in your car adapts to the quality and temperature of the outside air
These hybrid sensors have a more flexible implementation and allow less expensive installations and therefore a faster ROI.
Benefits
• Localisation : the position is known and accessible to all. This function allows a significant saving of time by completely eliminating the moments of research and unnecessary trips on site. An important operation is planned in the coming days; the team immediately knows where the equipment is available on site to carry out the intervention.
• Providing information directly in the field, without having to go through a label or a printable form (Paperless)) thanks to a display integrated into the sensor and provides dynamic management in real time of needs. A batch / product whose priority level is revised upwards can be prioritized live, its position and the information displayed on it being updated remotely without intervention.
• Real-time information collection:Tracking information for operations uploaded manually to a tracking sheet or a workstation is now collected automatically. So when a machine or a space remains occupied longer than expected and impacts the organization of production; you can simply redirect the flow to an alternative solution. Real-time updated information and people in the field visualize the change live on the object.
RTLS was a first step because it only implemented one technology. Because the needs within the same site can be multiple, hybrid RTLS is a more mature and efficient solution and brings you the right technological solution in the right place at the right time and with an optimized overall cost.
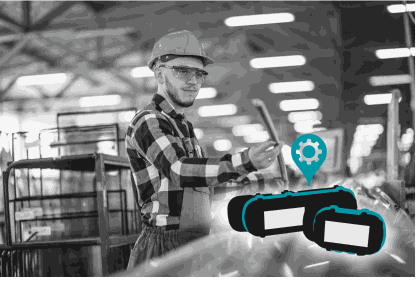
Agility and performance
The complete solution to switch to a real real-time control of your business exists, it is at your fingertips. Do you have an ERP and / or MES and your production is organized by production orders? Then hybrid RTLS will bring you value.
IIoT EDITAG Sensors are based on the exclusive multi-technology and multi-standard mOOnTAG® technology and adapt automatically without user intervention; Native hybrids, they are the only ones to cover the 3 mentioned localization approaches. This achieves the high level of reliability and performance demanded in an industrial environment.
More and more industrial sites are equipping themselves with this IIoT solution, fully entering the era of Industry 4.0. We measure productivity gains of 12% on most of the installations carried out.
In fact, do you remember how you lived before GPS? The same will apply to your future industrial installations and very soon.