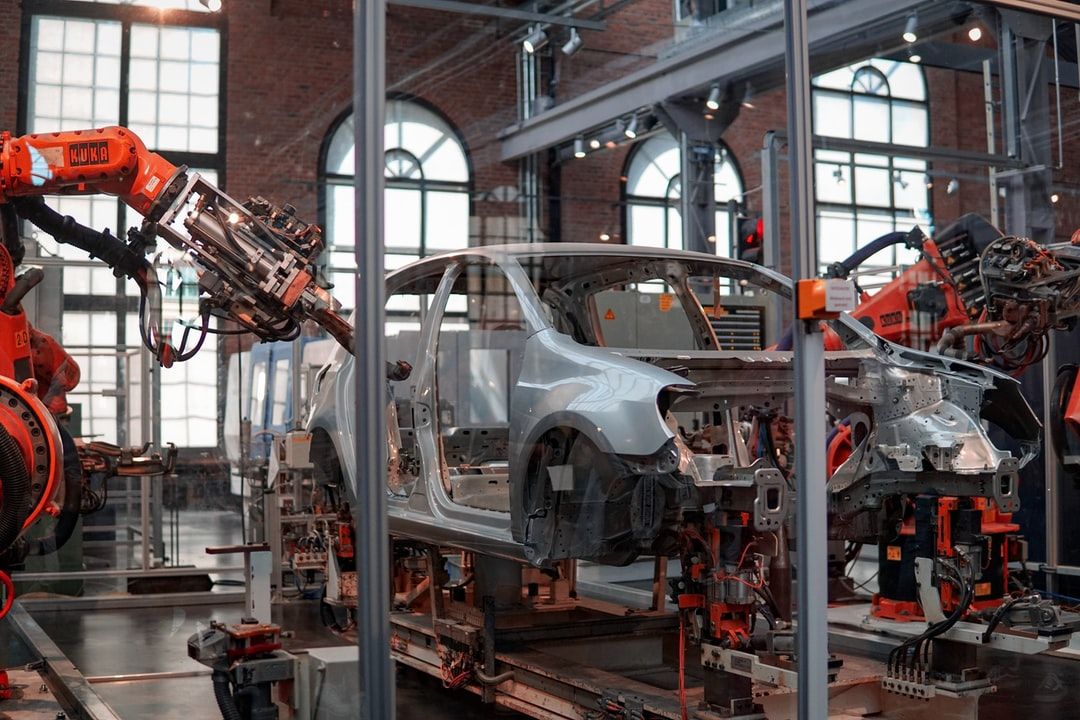
« You can’t manage what you don’t measure » W. Edwards Deming
n a Lean manufacturing and continuous improvement (Kaizen) approach, manufacturers must be able to identify pain points in order to establish flexible, real-time production processes and avoid waste.
It is essential for manufacturers to have real-time visibility of what is happening on the field.
SMEs, mid-caps, large accounts, all are concerned by this need for traceability, from storage to the final assembly stages.
IoT technologies provide a concrete answer to these challenges of continuous improvement.
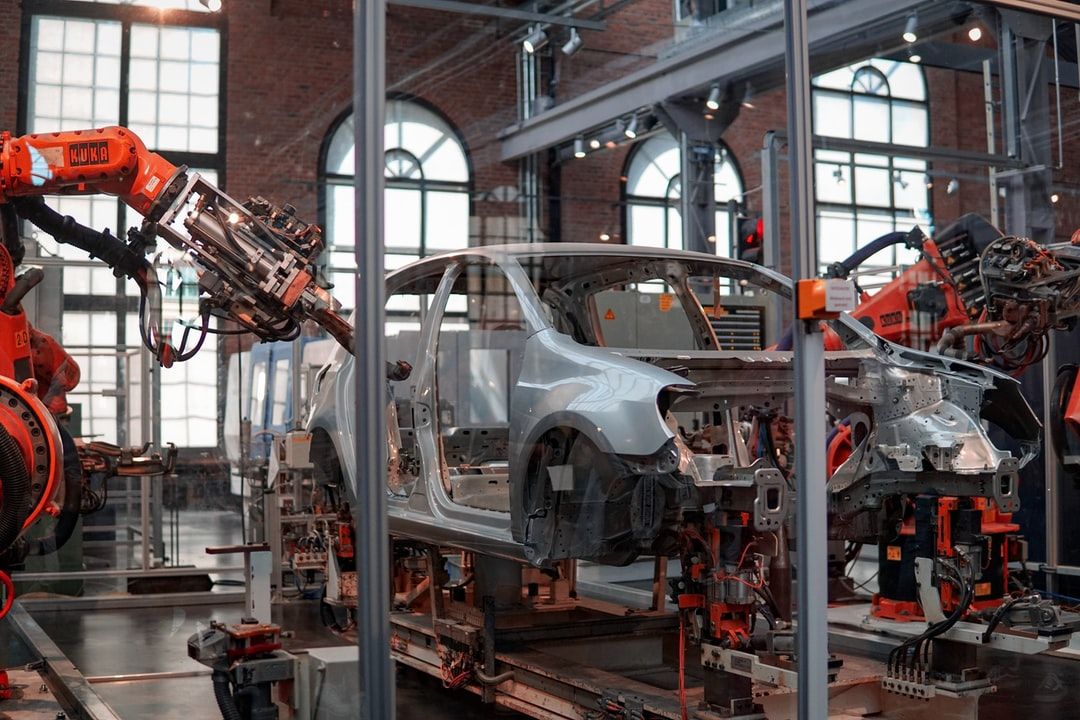
The digital twin, a real opened window onto the field
The consulting firm Gartner ranks the digital twin among the top 10 technology trends. Gradually it became part of the global industrial landscape. Today, few companies exploit the capabilities of the digital twin, but those that do, they anchor it in their IoT strategy for real exploitation by 2022.
The very concept of digital twin is most often associated and used as a simulation tool.
At EDITAG, our vision, supported by feedback from our industrial customers, encompasses the notion of digital twin to the operational.
In fact, IoT solutions are a source of real-time information that provides a “digital” representation of reality to control their processes as accurately as possible.
How it works?
The IoT becomes the data provider for the digital twin.IoT sensors placed in the field provide real-time information about location, material tracking, work-in-progress traceability, etc.
The digital twin is therefore constantly supplied with concrete data.
In addition to real-time visibility of field operations, the digital twin also offers predictions on upcoming events. An ideal solution therefore to anticipate breakdowns or ruptures and make the right decisions.
IIt must be understood that the IoT and the digital twin can work quite independently. The IoT alone makes it possible to trace the information necessary for the optimal functioning of a factory and the digital twin can exist without it.
The IoT finally enables the deployment of a whole new concept of digital twin. The digital twin then becomes a steering interface, a dynamic dashboard, a perfect reflection of what is happening on the field.
Other technologies could also be interfaced such as artificial intelligence or virtual and augmented realities …
We note once again that the IoT allows to discover new use cases within parallel technologies and this trend is far from weakening!