
How to guarantee a return on investment – ROI – fast?
When it comes to tracking and locating production orders, tools, production batches … in manufacturing companies, it often turns out that the initial investment to put the system in place can be high and this fact lessens the possibilities of return on investment.
How can this entry ticket be reduced without making any concessions on functionality, performance, reliability and quality of service?
Investments that sleep …
On the various projects carried out in manufacturing industries, we have observed percentages ranging from 10 to 50% of unused handling units. These are bins, pallets, trolleys, all types of handling units (MU) or even custom support allowing the transport of the manufactured assemblies. The more varied the productions and the more complex the products, the more handling units are simply stored and awaiting allocation. A conservative estimate would be an average of around 25% of unused assets.
However, the very principle of “track & trace” is that nothing is correctly traced if everything is not identified and followed.
With conventional methods and technologies, it would be necessary to place a geolocation beacon on each of the handling units (MU). This implies that 25% of this installation is non-productive because it is simply waiting on unused UMs. An unacceptable percentage in terms of financial management, asset immobilization and ROI optimization.
The solution: hybrid identification.
The EDITAG Industries solution is built on a unique patent for a hybrid and modular IoT sensor.
Basically, all handling units are equipped with a unique identifier, not an expensive geolocation tag, but a simple RFID tag, the mOOnTAG ID. This makes it possible to equip all the MUs at low cost.
Then, only when the UM is active, the operator adds to the mOOnTAG ID the geolocation sensor called mOOnTAG SENSOR.
Result: 25% reduction on the initial investment to start your “track and trace” project!
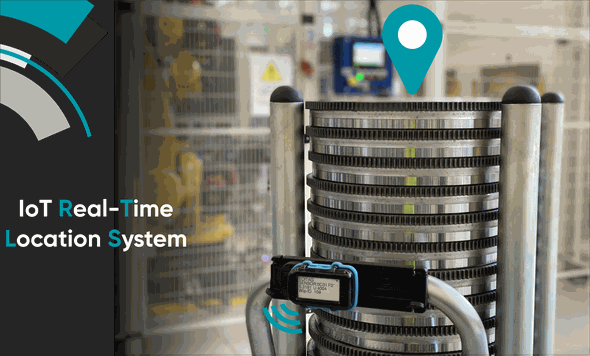
Digitize an operational gesture.
Clipping the mOOnTAG SENSOR onto the ID is information that is automatically fed back into the information system. The user therefore has real-time visibility of the state of his MUs, he knows if they are used and where they are located.
The operator does not need to enter the information since it is the mOOnTAG clip that triggers the alert. His gesture is digitized.
Then, once equipped with its complete mOOnTAG, the UM follows its cycle within the factory. All the important stages or passages to different islands are automatically fed back into the information system.
Interfaced with an ERP, MES or WMS, the application offers unparalleled real-time visibility of activities. The history and timestamp of these clips / unclips also make it possible to optimize the management of workshops.
A hybrid IoT track and trace solution therefore offers several advantages:
- a reduced initial investment compared to conventional technologies,
- a faster return on investment,
- an adoption by field teams guaranteed thanks to the digitized business activity,
- a real-time visibility of workshop activities.