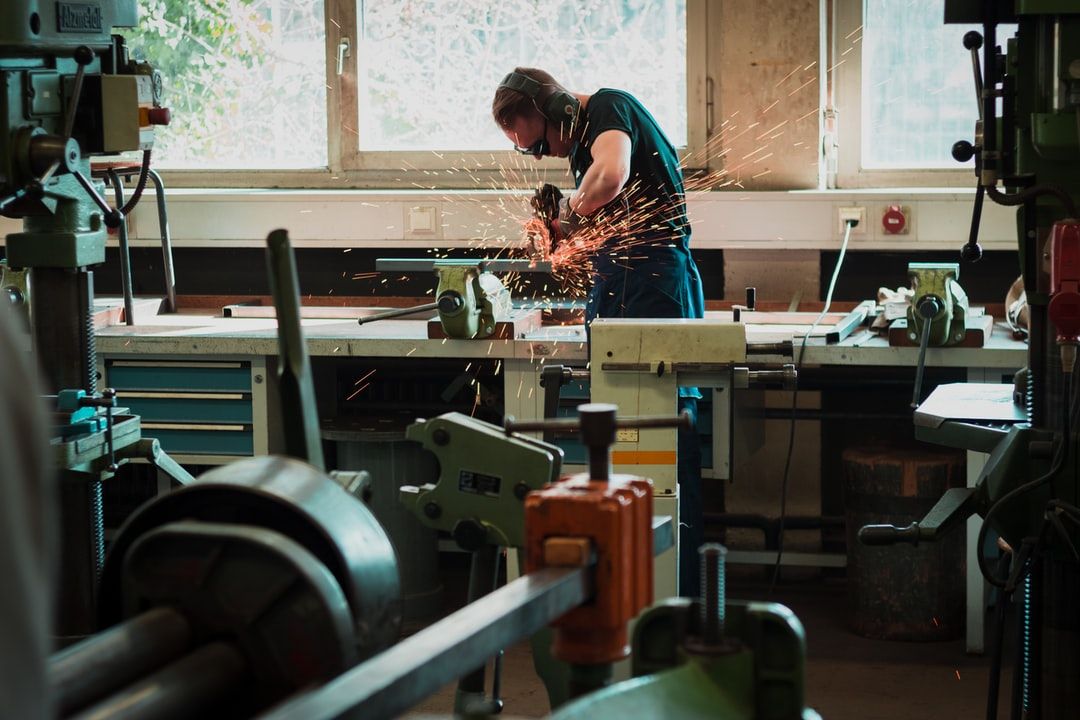
*Real Time Location System
Le pilotage des flux industriels consiste à organiser le déplacement de la matière, ou des en-cours de production, au cours du processus de fabrication afin d’obtenir la meilleure performance possible (productivité, TRS, temps de cycle, stock…).
Le degré de complexité varie d’une usine à l’autre en fonction du nombre d’opérations à réaliser, du mix produit, de l’organisation de l’espace de production et des contraintes logistiques imposées par les produits ; en effet les contraintes de production pour une montre, une voiture ou un engrenage d’une tonne sont différentes.
Cette complexité génère des situations imprévues dans la planification initiale des opérations qui se matérialisent par la recherche des en-cours sur site et un manque de visibilité globale sur l’état d’avancement de la production.
Quelle est la solution aujourd’hui pour finir à temps ses ordres de fabrication ?
Les réponses mises en place jusqu’à présent pour gérer la complexité d’organisation de production ont été de 2 ordres :
• Logiciel : Les systèmes type ERP et MES depuis les années 80, ont permis de prendre en compte un nombre plus important de critères dans l’organisation de production. Il est devenu possible de gérer des situations et des flux toujours plus complexes et d’être au plus proche de la réalité.
• Organisationnel : le développement progressif de l’approche Lean depuis les années 50 et plus particulièrement depuis la fin des années 90 a permis de prendre en compte la réalité du terrain afin de s’y adapter. Cela a donné lieu à la mise en place de solutions comme l’adaptation du poste de travail, de chaines de fabrication en U, la réduction des mouvements inutiles, les kanban, la prise en compte des temps masqués…
L’un des principaux challenges dans les déploiements de solutions ERP/MES est de garantir la parfaite adéquation entre le « physique », et « l’informatique ».
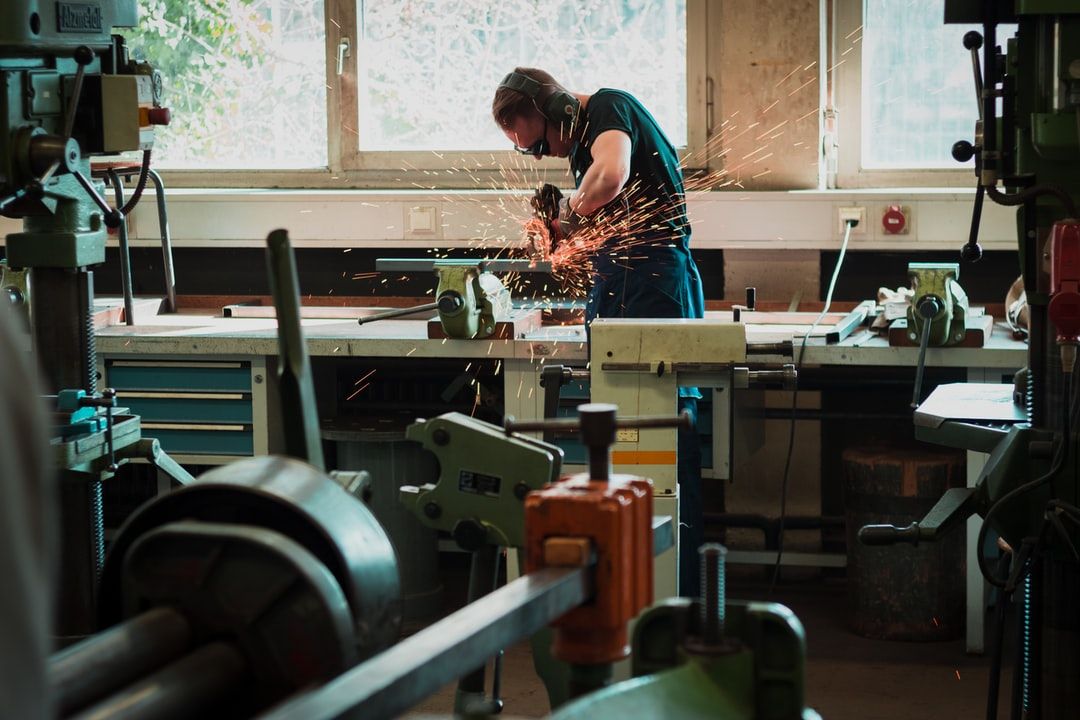
Aujourd’hui il y a un mode d’organisation qui permet de gagner en efficacité en se basant sur la récupération automatique des informations de géolocalisation des objets qui comptent pour la production.
La fabrication peut alors être organisée à partir de données réelles et vérifiées rendant la prise de décision plus efficace : la notion de « pilotage » prend tout son sens. Le cadencement des tâches et la réaction aux aléas sont réalisés avec des informations à jour et en anticipant le déroulement des prochaines actions. Par exemple un poste de travail démarre ses opérations en sachant que dans 10 minutes le prochain lot de pièces sera livré. Ou encore, un opérateur d’une machine outils passe à l’ordre de fabrication suivant car il est informé que la pièce qui était prévu à l’instant T est encore de l’autre côté de l’usine. Le convoyage des pièces peut être anticipé de même que la mise à disposition d’outillage spécifique.
Il faut ajouter à cette information de localisation la possibilité d’échanger de manière digitale l’information avec les utilisateurs. L’information est rendue accessible directement là où elle est utilisée, sur le terrain, sans passer par l’intermédiaire d’un document imprimé ou d’un poste de travail.
Cette organisation de la production « en temps réel », ce pilotage, se basent sur les technologies RTLS (Real Time Location System) qui reposent sur la mise en œuvre d’identifiant actif ou passif (IIoT – industrial IoT) et d’une infrastructure radio.
L’identifiant actif, équipé d’une batterie, communique de façon autonome avec le système radio. Il se distingue de l’identifiant passif tel que le tag RFID qui a besoin de recevoir un signal extérieur pour renvoyer de l’information. Il y a plusieurs technologies radio, celles permettant de localiser les objets (UWB, BLE) et celles de la communication sur des réseaux radio industriels robustes ou sur des réseaux très longue portée/très faible consommation d’énergie comme LORA.
Chaque objet à suivre est muni d’un identifiant. L’objet (en-cours/outillage) est pris en compte en temps réel dans l’organisation de la production. Afin de valoriser les données issues des capteurs l’infrastructure radio est connectée aux différents logiciels métiers pour échanger l’information nécessaire. Les technologies principales de géolocalisation en intérieur existent depuis plusieurs années ce qui leurs a permis d’atteindre un niveau de maturité de et de fiabilité pour être utilisées dans l’industrie.
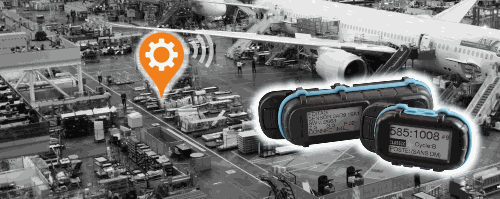
Il existe aujourd’hui 3 façons de suivre les flux :
Triangulation : l’objet est équipé d’un capteur actif – le système détermine la position de l’objet en temps réel (RTLS) par rapport à des antennes dont la position est connue, comme pour la technologie UWB par exemple. Très précise cette solution nécessite en revanche la pose de plusieurs antennes pour mailler la zone de déplacement des objets. Les coûts de mise en œuvre sont les plus élevés par rapport aux autres solutions.
Zoning : l’objet est équipé d’un capteur actif – une balise radio, similaire au beacon BLE ou une borne WIFI, émet un signal périodique avec une portée réglable. Le capteur qui reçoit ce signal sait qu’il est entré dans la zone de la balise (un lieu de stockage, un ilôt de production, un lieu de passage typiquement) ; l’absence de réception du signal lui permet de savoir qu’il en est sorti. Le capteur communique cette information en temps réel. Cette solution est la plus facile à configurer /reconfigurer car il suffit d’allumer la balise à l’endroit souhaité pour que le système soit opérationnel. De plus ce système ne nécessite pas de câblage réseau pour fonctionner ce qui représente une économie importante lors de la mise en œuvre de la solution.
Détection de passage : l’objet est équipé d’un identifiant passif – le système est composé de portiques ou points de passage RFID qui lisent l’identifiant à chaque passage. Cette solution offre l’avantage de pouvoir fonctionner dans des environnements où les capteurs actifs ne peuvent pas encore aller et permettre l’identification en masse lorsqu’il y a un grand nombre d’objets à détecter simultanément. Il existe un très large choix d’identifiants RFID bon marché, capable de fonctionner dans pratiquement tous les environnements mais la solution nécessite l’installation de portiques à des endroits déterminés dont la mise en œuvre peut s’avérer coûteuse.
Le tableau ci-dessous, résume les différentes approches possibles :
Portique RFID |
Zoning |
Triangulation | |
Précision de localisation | NA | 1m-30m | <1m |
Type de localisation | Points de passage |
Points de passage
Point pré-déterminés
|
Tous |
Détection passage en masse | + | = | = |
Mise en oeuvre | = | + | – |
Interaction utilisateur | NON | OUI | OUI |
Autres capteurs (température, choc…) | NON | OUI | OUI |
Chaque application à ses avantages et ses inconvénients et c’est la façon de les mettre en œuvre qui donne le niveau de performance final et de création de valeur de la solution.
Récemment sont apparus des capteurs hybrides qui mettent en œuvre plusieurs technologies en même temps afin de couvrir le plus largement les cas d’utilisation sur le terrain, et ajouter de nouvelles fonctions comme des écrans, c’est une solution RTLS hybride.
La configuration et les besoins de chaque industriel sont différents et même au cœur de la même installation, les besoins peuvent varier d’un poste à l’autre. La solution technologique doit s’adapter en mettant en œuvre la bonne technologie au bon moment et se plier aux besoins des processus et ne pas obliger les processus a des concessions dues aux limites de la technologie ; comme la climatisation automatique de votre voiture s’adapte à la qualité et la température de l’air extérieur.
Ces capteurs hybrides ont une mise en œuvre plus souple et permettent des installations moins coûteuses et par conséquent un ROI plus rapide.
Bénéfices
• Localisation : la position est connue et accessible à tous. Cette fonction permet de réaliser d’importante économie de temps en éliminant complètement les moments de recherches et les déplacements inutiles sur site. Une opération importante est prévue dans les jours qui arrivent ; l’équipe sait immédiatement où sont les équipements disponibles sur site pour mener à bien l’intervention.
• Apport d’information directement sur le terrain, sans devoir passer par une étiquette ou un formulaire à imprimer (Paperless) grâce à un afficheur intégré au capteur et donne une gestion dynamique en temps réel des besoins. Un lot/produit dont le niveau de priorité est revu à la hausse peut être priorisé en direct, sa position et l’information affichée dessus étant mise à jour à distance sans intervention.
• Remontée d’information en temps réel : Les informations de suivi des opérations remontées manuellement sur une fiche suiveuse ou un poste de travail sont maintenant collectées automatiquement. Ainsi lorsqu’une machine ou un espace reste occupé plus longtemps que prévu et impacte l’organisation de la production ; vous pouvez simplement rediriger le flux vers une solution alternative. L’information mise à jour en temps réel et les personnes sur le terrain visualise le changement en direct sur l’objet.
Le RTLS était une première étape car il ne mettait en œuvre qu’une seule technologie. Parce que les besoins au sein d’un même site peuvent être multiple, le RTLS hybride est une solution plus mature et performante et vous apporte la bonne solution technologique au bon endroit au bon moment et avec un coût global optimisé.
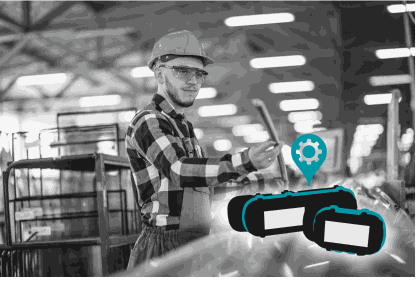
Agilité et performance
La solution complète pour basculer dans un réel pilotage en-temps réel de votre existe, elle est à portée de main. Vous avez un ERP et ou MES et votre production est organisée par des ordres de fabrication ? Alors le RTLS hybride va vous apporter de la valeur.
Les CAPTEURS IIoT EDITAG reposent sur la technologie exclusive mOOnTAG® multi-technologie et multi-standard et s’adaptent de façon automatique sans intervention de l’utilisateur ; nativement hybrides, ils sont les seuls à couvrir les 3 approches de localisation évoquées. Cela permet d’atteindre le niveau de fiabilité et de performance élevé exigé dans un environnement industriel.
De plus en plus de sites industriels s’équipent de cette solution IIoT, s’inscrivant pleinement dans l’ère de l’industrie 4.0. Nous mesurons des gains de productivité de 12% sur la plupart des installations réalisées.
En fait, vous rappelez vous comment vous viviez avant le GPS ? Il en va en être de même de vos futures installations industrielles et très prochainement.